Bearing assembly with Torque-Motor
Type LTD

Franke bearing assemblies with integrated direct drive (torque motor) are characterized by high dynamics, maximum energy efficiency and a compact installation space combined with center-free design.
Description
Bearing assemblies with direct drive are suitable for applications where high performance and low space requirements are important criteria. The integration of the drive into the bearing housing means that wear-prone assemblies for transmitting drive power, such as toothed belts, shafts or chains, can be dispensed with. This reduces the required drive energy and also benefits more accurate positioning.
Properties - Evaluation
Accuracy | |
Speed | |
Ø-Range | |
Price |
Technical data
Material
C45N (optionally aluminium)
Operating temperature
-10 °C to +80 °C
Mounting position
Any
Lubricant
With bearing grease via grease nipple
Options
Absolute measuring system, axial cable outlet, control units incl. cables, water-cooling
Technical advice
Super compact and super individual: Franke direct drive with torque motor LTD
Basic-Data
- Housing steel or aluminium
- KKØ: 100 - 1800 mm
- Incremental measuring systems
- Absolute measuring systems
The advantages
- Compact design
- Large centre clearance
- Free choice of components
- Four standard sizes from stock
- Customised solutions
Function & benefits:
Compact
Dynamic
Energy efficient
Compact design, large centre clearance
Franke bearing assemblies with integrated direct drive (torque motor) are characterized by high dynamics, maximum energy efficiency and a compact installation space combined with center-free design.
Available diameters
Franke bearings with direct drive are available in diameters from 100 mm to 1,800 mm.
Whitepaper slewing ring with torque drive
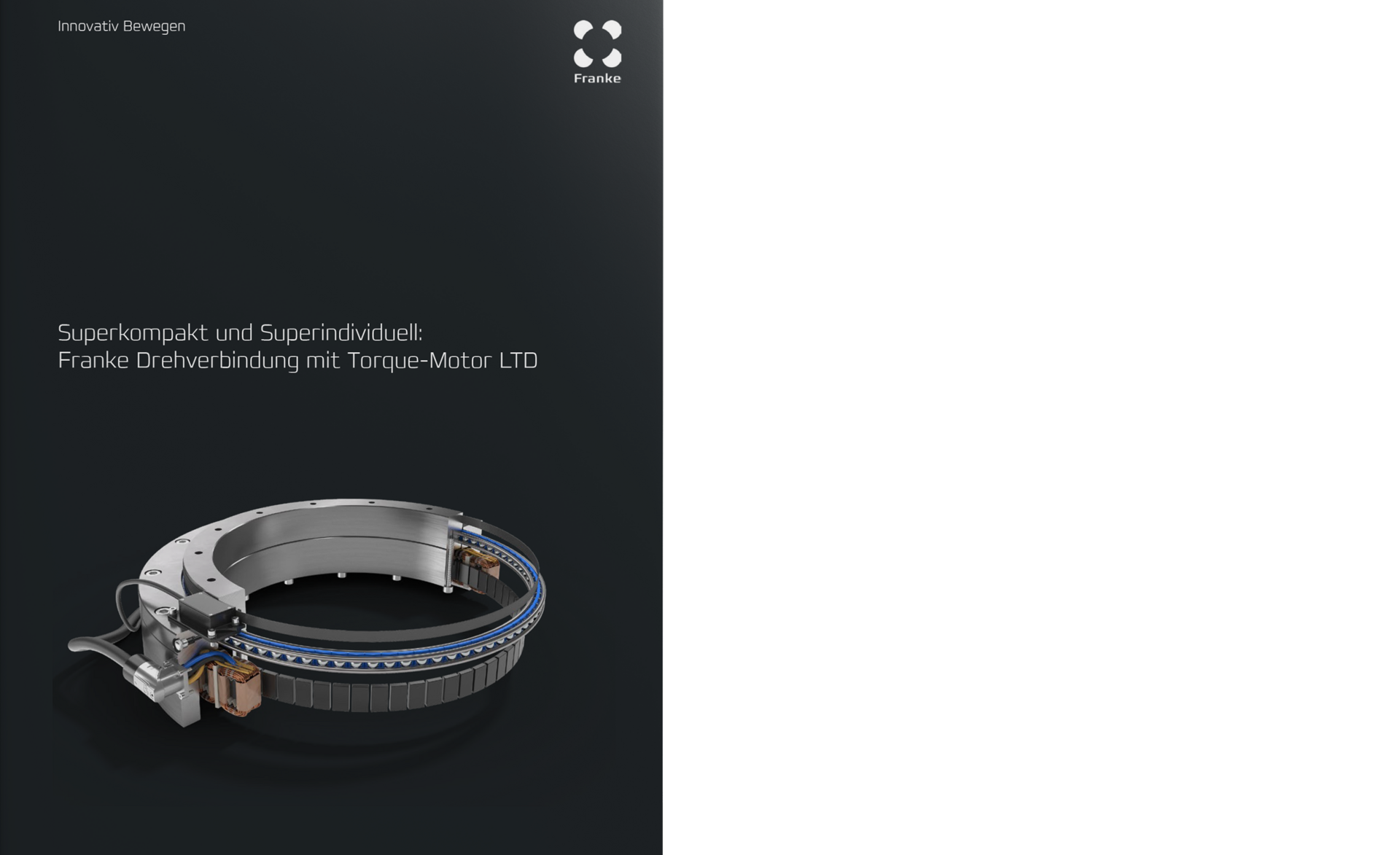
Find out more about slewing rings with integrated torque motor and why it is superior to other drive types in almost every respect.
In future, dispense with components such as gearboxes and drive pinions.
Data tables
Compare data and calculate load cases

LTD0100 | MyFranke | |||||||||||
---|---|---|---|---|---|---|---|---|---|---|---|---|
Name | ΚΚØ mm |
Load ratings kN |
Torque Nm |
Power A |
Speed 1/min. |
Weight kg |
CAD-Download Calculate loads |
|||||
C0a | C0r | Ca | Cr | MNom | MPeak | INom | IPeak | nmax | ||||
LTD-0100 | 100 | 46 | 22 | 17 | 14 | 4,5 | 16 | 1,8 | 7 | 2140 | 8,0 |
Register now to get |


LTD0215 | MyFranke | |||||||||||
---|---|---|---|---|---|---|---|---|---|---|---|---|
Name | ΚΚØ mm |
Load ratings kN |
Torque Nm |
Power A |
Speed 1/min. |
Weight kg |
CAD-Download Calculate loads |
|||||
C0a | C0r | Ca | Cr | MNom | MPeak | INom | IPeak | nmax | ||||
LTD-0215 | 215 | 128 | 60 | 26 | 22 | 26,4 | 105 | 3,1 | 12,8 | 640 | 21,0 |
Register now to get |


LTD0320 | MyFranke | |||||||||||
---|---|---|---|---|---|---|---|---|---|---|---|---|
Name | ΚΚØ mm |
Load ratings kN |
Torque Nm |
Power A |
Speed 1/min. |
Weight kg |
CAD-Download Calculate loads |
|||||
C0a | C0r | Ca | Cr | MNom | MPeak | INom | IPeak | nmax | ||||
LTD-0320 | 320 | 382 | 180 | 45 | 39 | 77 | 329 | 4,3 | 21,6 | 300 | 44,0 |
Register now to get |


LTD0385 | MyFranke | |||||||||||
---|---|---|---|---|---|---|---|---|---|---|---|---|
Name | ΚΚØ mm |
Load ratings kN |
Torque Nm |
Power A |
Speed 1/min. |
Weight kg |
CAD-Download Calculate loads |
|||||
C0a | C0r | Ca | Cr | MNom | MPeak | INom | IPeak | nmax | ||||
LTD-0385 | 385 | 458 | 216 | 48 | 41 | 118 | 522 | 4,3 | 21,7 | 193 | 57,0 |
Register now to get |

Power comparison | LTD-0100 | LTD-0215 | LTD-0320 | LTD-0385 | ||
---|---|---|---|---|---|---|
Nominal Data (free air convection) |
||||||
Nominal Torque | TNomAC | Nm | 4,5 | 26,4 | 77 | 118 |
Nominal Current | INomAC | Arms | 1,8 | 3,1 | 4,3 | 4,3 |
Nominal Speed | nNomACLk | rpm | 2140 | 640 | 299 | 193 |
Nominal Power | NomAC | W | 1005 | 1770 | 2409 | 2386 |
Winding Losses1 | PVDAC | W | 54 | 131 | 230 | 309 |
Total Losses2 | PDAC | W | 96 | 179 | 295 | 357 |
Holding Torque | THAC | Nm | 3,2 | 18,7 | 54 | 83 |
Holding Current | IHAC | Arms | 1,2 | 2,2 | 3 | 3 |
Peak Data |
||||||
Peak Torque | TPeak | Nm | 16 | 105 | 329 | 522 |
Peak Current | IPeak | Arms | 7 | 12,8 | 21,6 | 21,7 |
Speed at Peak Torque | nPeak | rpm | 1130 | 320 | 126 | 74 |
Peak Power | PPeak | W | 1897 | 3526 | 4343 | 4049 |
Winding Losses1 | PPeak | W | 863 | 2236 | 5886 | 7876 |
Total Losses2 | PDPeak | W | 877 | 2253 | 5904 | 7889 |
Power Data | ||||||
Torque Constant | kt | Nm/Arms | 2,549 | 8,51 | 18,037 | 27,449 |
Vrms/(rad/s) | 1,577 | 5,2 | 11,094 | 16,694 | ||
BEMF Constant (Phase - Phase) | ke | Vrms/(rpm) | 0,165 | 0,545 | 1,162 | 1,748 |
Motor Constant | km | Nm/vW | 0,459 | 1,973 | 4,483 | 6,25 |
Idle Speed | nidle | rpm | 2390 | 727 | 340 | 226 |
max. Speed (Fieldweaking) | nmax | rpm | - | - | - | - |
max. Frequency (Idle/Fieldweaking) | fmax | Hz | 398 | 254 | 159 | 124 |
DC Bus Voltage | UDC | VDC | 560 | 560 | 560 | 560 |
Ø Resistance per Phase (winding only) | RPh20 | Ω | 4,419 | 3,457 | 3,206 | 4,235 |
Ø Inductance per Phase (winding only) | LPh | mH | 21,727 | 19,532 | 21,071 | 28,049 |
electr. Time Constant t=L/R | Tel | ms | 4,92 | 5,65 | 6,57 | 6,62 |
Number of Polepairs | n | 10 | 21 | 28 | 33 | |
Winding Connection | Star | Star | Star | Star | ||
Measuring System | ||||||
Measuring Method | incremental | |||||
Reference mark | single coded | |||||
Measuring principle | inductive | |||||
Interface | 1 Vss | |||||
Cable length | 1 m | |||||
Grating period | 1000 µm | |||||
Line count | 256 | 640 | 938 | 1200 | ||
Interpolation | 10-fold | |||||
Number of signal periods | 2560 | 6400 | 9380 | 12000 | ||
Position error per grating period | ±11" | ±4,5" | ±3" | ±2,5" | ||
Grating period accuracy (±10µm arc length) | ±51" | ±20" | ±14" | ±11" | ||
Max. scaning frequency | 40 kHz | |||||
Voltage supply | 4V to 7V DC | |||||
Electrical connection | cable with M23, 12 pin male |
Annotations
1 Winding Losses are referred to a Coil Temperature of 100°C.
2 The total Losses are made up of: Winding Losses; Stator Iron Losses; Rotor Losses;
Calculation of total Losses: Winding Losses + Stator Iron Losses (at speed X) + Rotor Losses (at speed X)
Ensure that your servo drive can handle the Nominal- and Peakcurrent of the Motor. An adjustment of the Speed and DC Bus Voltage can be done after consultation. The nominal data in this datasheet are based on an ambient/coolant temperature of 20°C.
The stated nominal Torques are without consideration of friction losses through Bearings or Sealings.
Because the exact duty type depends also on the thermal connection of the motor, the embedded thermal monitoring system has to be analysed and attented. However, attention has to be payed that the temperature sensors do not show the exact temperature of the winding and this could be up to 20 K higher due to thermal capacities. Despite an electrical insulation towards the winding, you are only allowed to connect the sensors to your controller by using a galvanic separation in between.