Customer Stories
Franke solves challenging rotation task for vegetable spiral cutters from company Kronen
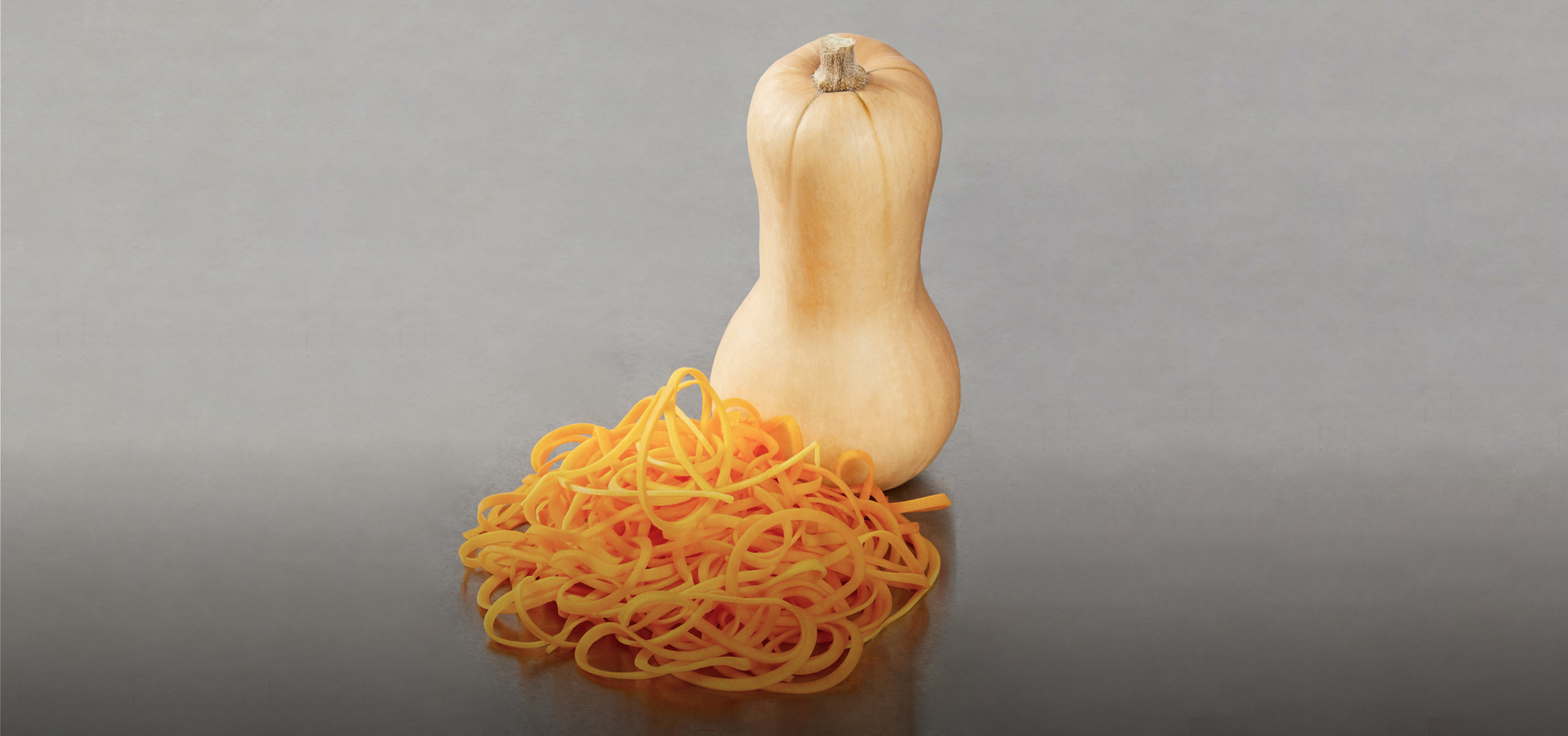
A challenge becomes a success story: After previously working on a solution with several suppliers, Kronen GmbH finally found the partner in Franke who mastered a difficult rotation task with a sophisticated bearing assembly.
Kronen develops and produces machines and complete lines for processing food - these include functions for cutting, washing, peeling and packaging, among others. "The quality and advisory competence of our company is appreciated all over the world. Accordingly, the bar is set high. Our customers find the right machines from us for the products they process," explains Sebastian Serrer, design engineer at Kronen.
Demanding conditions for bearings
One of these machines is the SP150 spiral cutter, which cuts fruit and vegetables into long spaghetti-shaped strips. „At high speed, it turns a butternut squash with a diameter of 15 cm into a 16-metre spiral, for example," says Sebastian Serrer. Another possible application is low-carbohydrate vegetable noodles - currently very trendy.
Building a machine that can perform this artistic cutting style is no easy matter. This also applies to the integration of supplied components. For example, specific requirements were placed on the roller bearing that guides the cutting tool. The temperature development was particularly critical here. Strong heating of the roller bearing would have impaired the quality of the processed food and therefore had to be avoided at all costs.
In addition, other challenges had to be overcome: "In the first tests with conventional bearings, dirt kept getting into the bearings," recalls design engineer Sebastian Serrer. "There was also the problem that too much cleaning, for example with steam jets and jet water, damaged the bearings." However, hygiene standards in particular are of immense importance in the food industry. Larger cleaning intervals were therefore not a practicable solution.
Profile of the Franke solution
Taylor-made Franke bearing assembly
Application in food processing
Special challenges: Avoiding heat build-up, frequent and intensive cleaning
Bearing requirements:
Speed, hygiene, tightness, smooth running and long service life
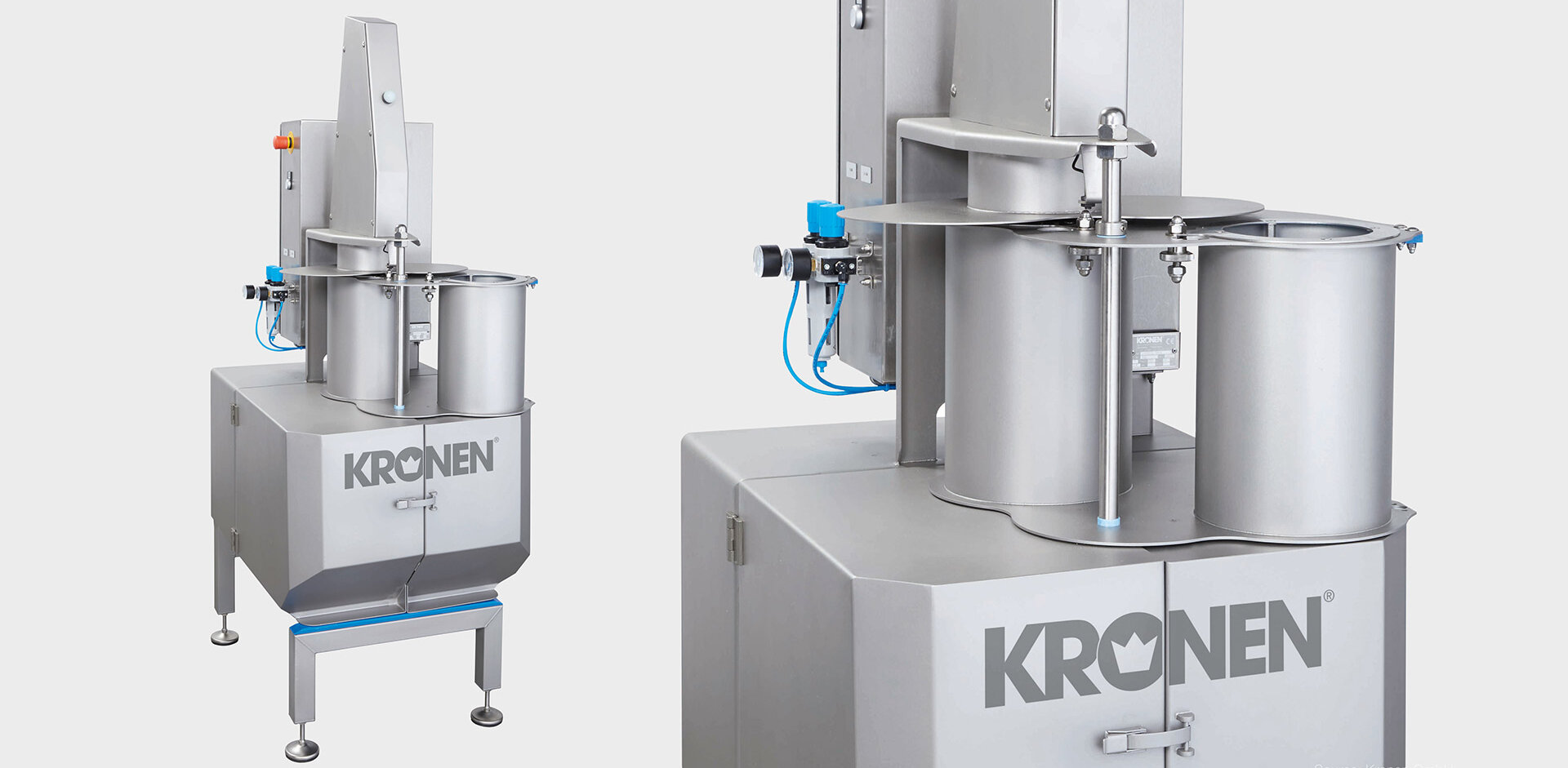
Franke with a new design approach
Where standard bearings reach their limits due to customer-specific requirements, Franke offers more advanced solutions with its flexibly adaptable wire-race bearings. In the case of the Kronen project, several problems had to be solved at the same time: heat generation, speed, hygiene, tightness, smooth running and long service life. Franke succeeded in meeting all these requirements with a customised bearing assembly using Franke wire-race bearing technology. The Franke bearing assembly guides the rotating cutting tool. The cut product is transported away through the center of the bearing assembly. The Franke solution is "the first that meets all the criteria and also lasts for a long time", explains Sebastian Serrer. "Moreover, the machine is very fast, the speed goes up to 690 rpm. It took some fiddling around and constructive ideas until we found a solution. Especially since we also had to deal with the problem of contamination and cleaning. The bearing had to be tight, otherwise the service life of the machine would be rapidly reduced," explains Michael Bärstecher, technical advisor at Franke.
For the specific requirements, we can offer unparalleled solutions. Solutions that are second to none.Michael Bärstecher, Franke field sales advisor
Labyrinth seal does not let through anything
After several tests, stainless steel proved to be the best material for the bearing. In order to protect it, for example during steam jet and water jet cleaning, a new design approach was required. The result: a labyrinth seal. This reliably prevents food residues, steam, water or cleaning agents from penetrating the bearing. An ingenious design that demonstrates Franke's strengths: "For the specific requirements, we can offer customised solutions that are second to none," says Michael Bärstecher.
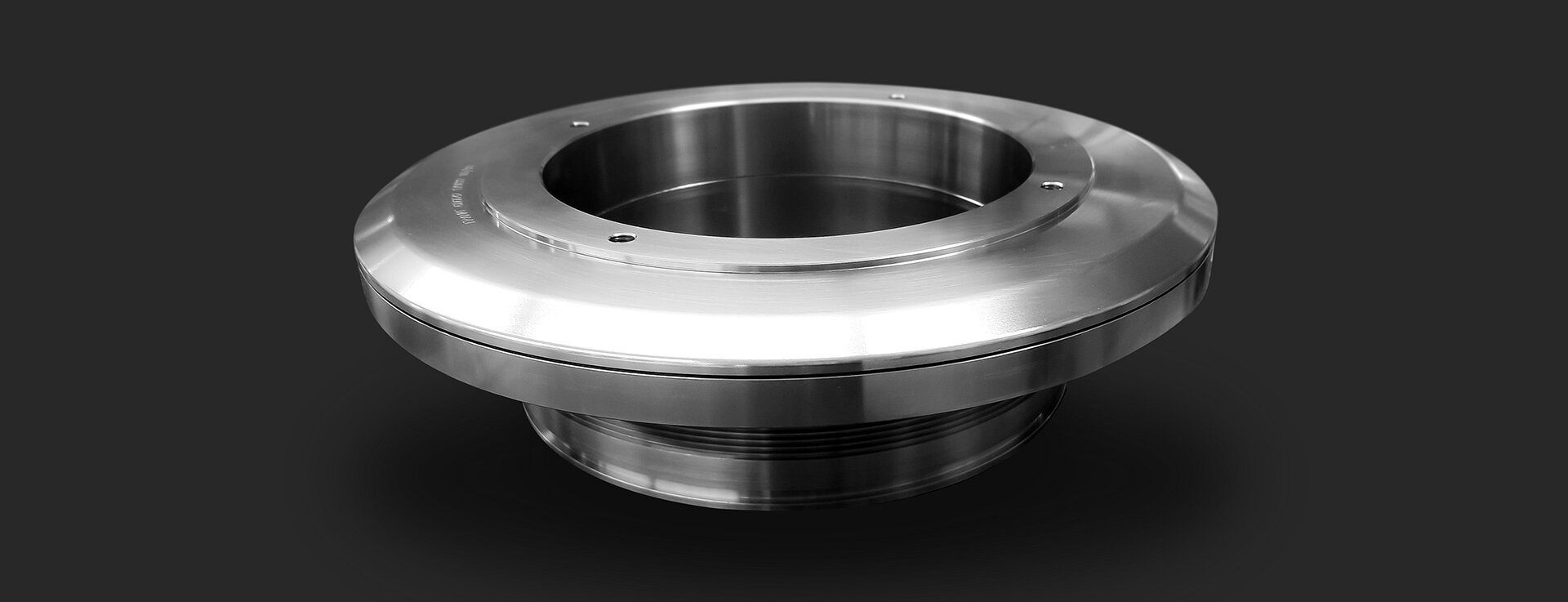
Passed the endurance test
The Franke design already proved its worth in the first practical test under particularly demanding conditions: "A Franke bearing assembly went to a customer for testing, who used it for 16 hours a day in an endurance run. After half a year, it looked as good as new," says Sebastian Serrer. The second prototype was tested directly at Kronen in a six-week 24-hour operation - without any problems. Afterwards, the bearing elements were as good as new - this led to the decision to equip the spiral cutters with Franke bearing assembly as standard.
More benefit through retrofit
The Franke design also has another benefit: if a bearing assembly reaches the end of its life cycle, it can simply be retrofitted. This results in a double benefit: lower costs and more sustainability. Because in the event of wear, the enclosing construction remains intact, only the bearing elements inside it have to be replaced.
Everything went quickly and smoothly, the solution and design proposals were targeted and precise.Sebastian Serrer, design engineer at Kronen
Cooperation runs like clockwork
"In Franke, we have found a partner with competence and excellent support," Sebastian Serrer sums up, "in all areas such as calculations, designs or with regard to relubrication intervals. Everything went quickly and smoothly, the solution and design proposals were targeted and precise. There was and is always an answer to questions. In short: it runs like clockwork, just like a good bearing - a literally smooth cooperation."
Profile of the Franke solution
Taylor-made Franke bearing assembly
Application in food processing
Special challenges: Avoiding heat build-up, frequent and intensive cleaning
Bearing requirements:
Speed, hygiene, tightness, smooth running and long service life
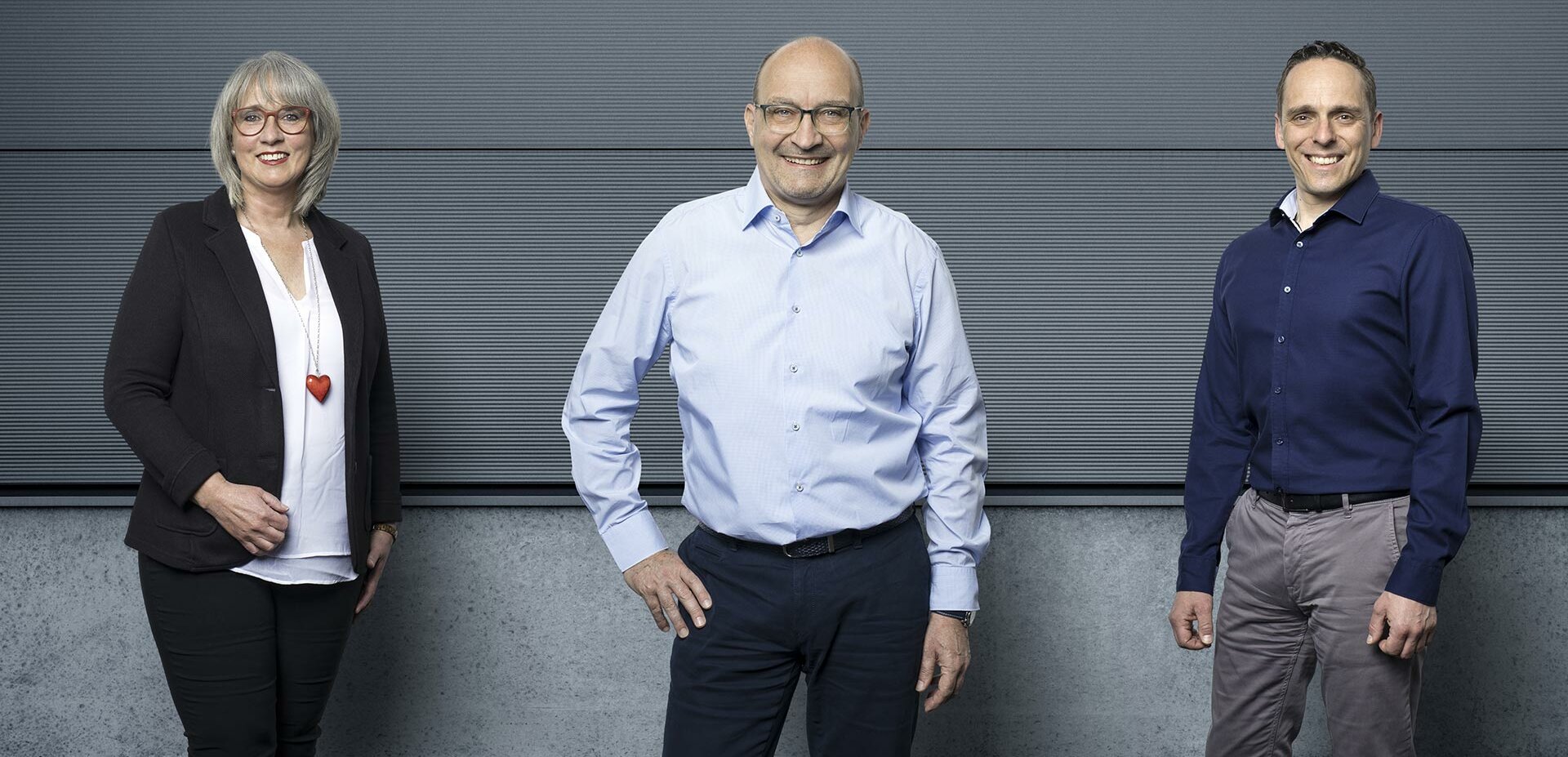
About Kronen
Kronen GmbH is one of the world's leading suppliers to the catering, convenience, fresh cut, delicacies and food industries with a focus on fruit, vegetable and salad processing. The company, based in Kehl am Rhein, develops and produces individual machines, special machines and complete processing lines for preparing, cutting, washing, drying, peeling, packaging and sterilising food, also on a large scale. Kronen GmbH was founded in 1978 and employs 120 people.