Customer Stories
Innovative winding technology for the ultimate electric car
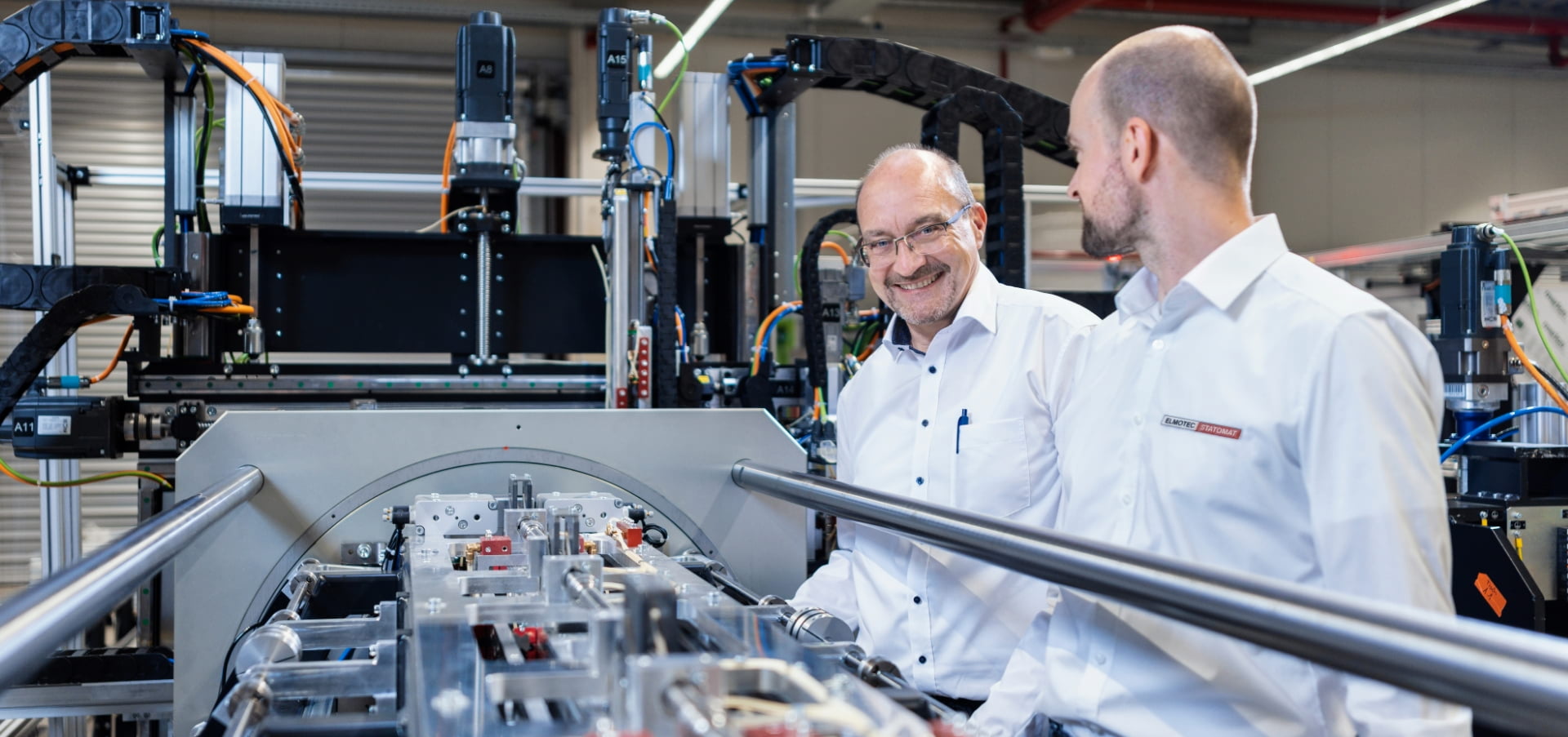
Schaeffler ELMOTEC STATOMAT stator winding machines are used to manufacture electric motors for the luxury and performance electric car industry. Schaeffler's innovative ELMOTEC STATOMAT technology makes it possible to tightly wind the copper coils to maximum performance and efficiency. In order to achieve the required precision, the design specialist from Schaeffler turned to Franke for the perfect bearing solution.
In this segment of the electric car industry, customers expect performance, efficiency and reliability. With a six-figure price tag, these vehicles have to be the best of the best and able to travel long distances between charges.
How do you build an engine that is half the size of current gasoline engines but delivers over 600 hp – for a car capable of over 1,000 hp? Schaeffler ELMOTEC STATOMAT delivers that solution. The German company, based near Frankfurt, has been part of the Schaeffler Group since 2019 and is the global leader in winding machines for the automotive, industrial and household appliance markets.
Leader in flat wire shaft winding
This mechanical engineering company is a pioneer and driver of innovation in this technological field. In order to build these super electric car engines, Schaeffler ELMOTEC STATOMAT mastered the process of flat wire wave shaft winding. Compared with the traditional hairpin process, the flat wire wave is processed into a continuously mesh, significantly reducing the number of welds which are the primary cause of motor failure. These more compact windings lower electrical loss and result in more power and reliability.
Profile of the Franke bearing assemblies used:
12 customer-specific Franke bearing assemblies with Ø 530/700/900 mm
Advantages used: precision, low weight, compactness, ready for installation
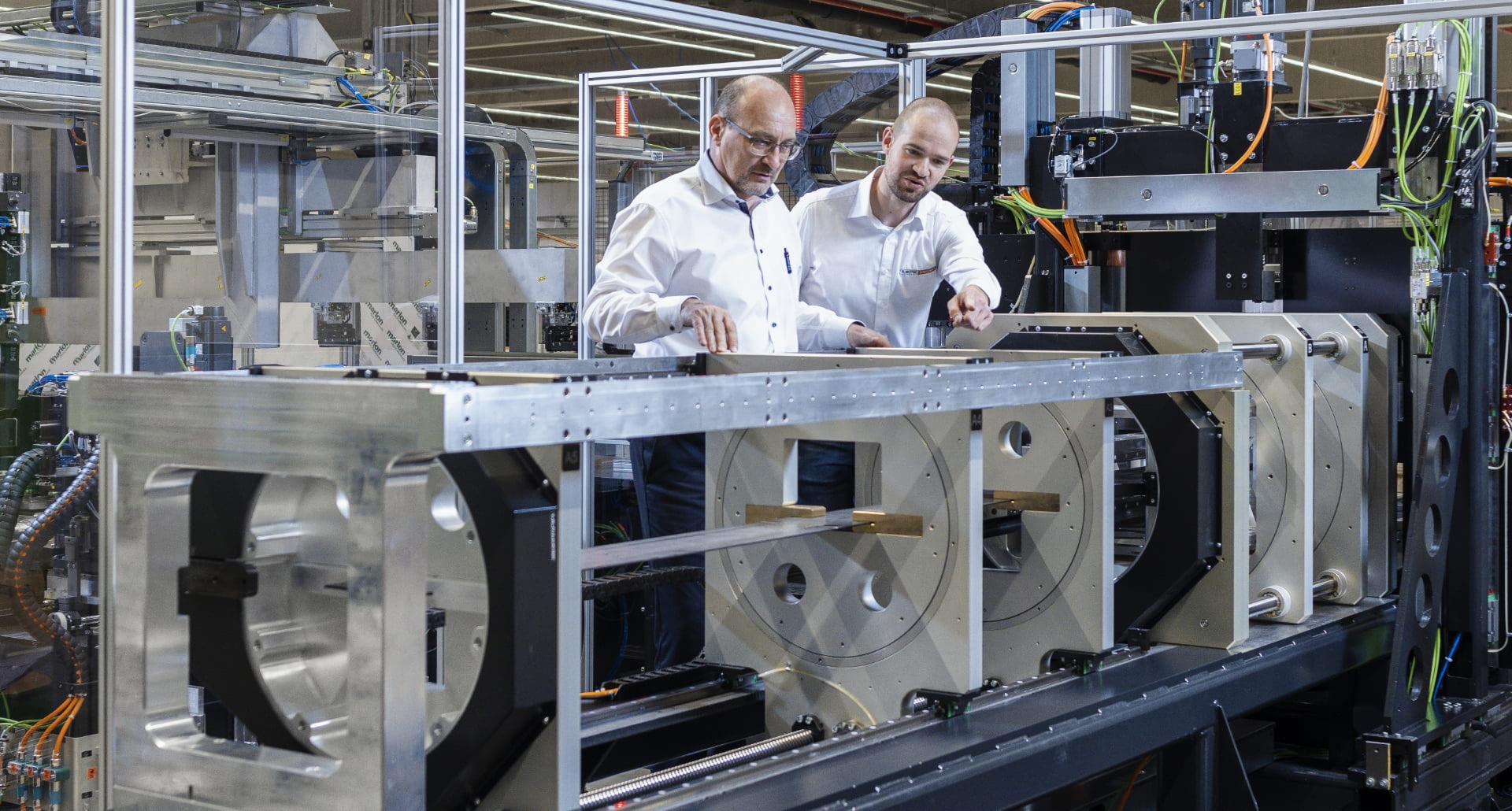
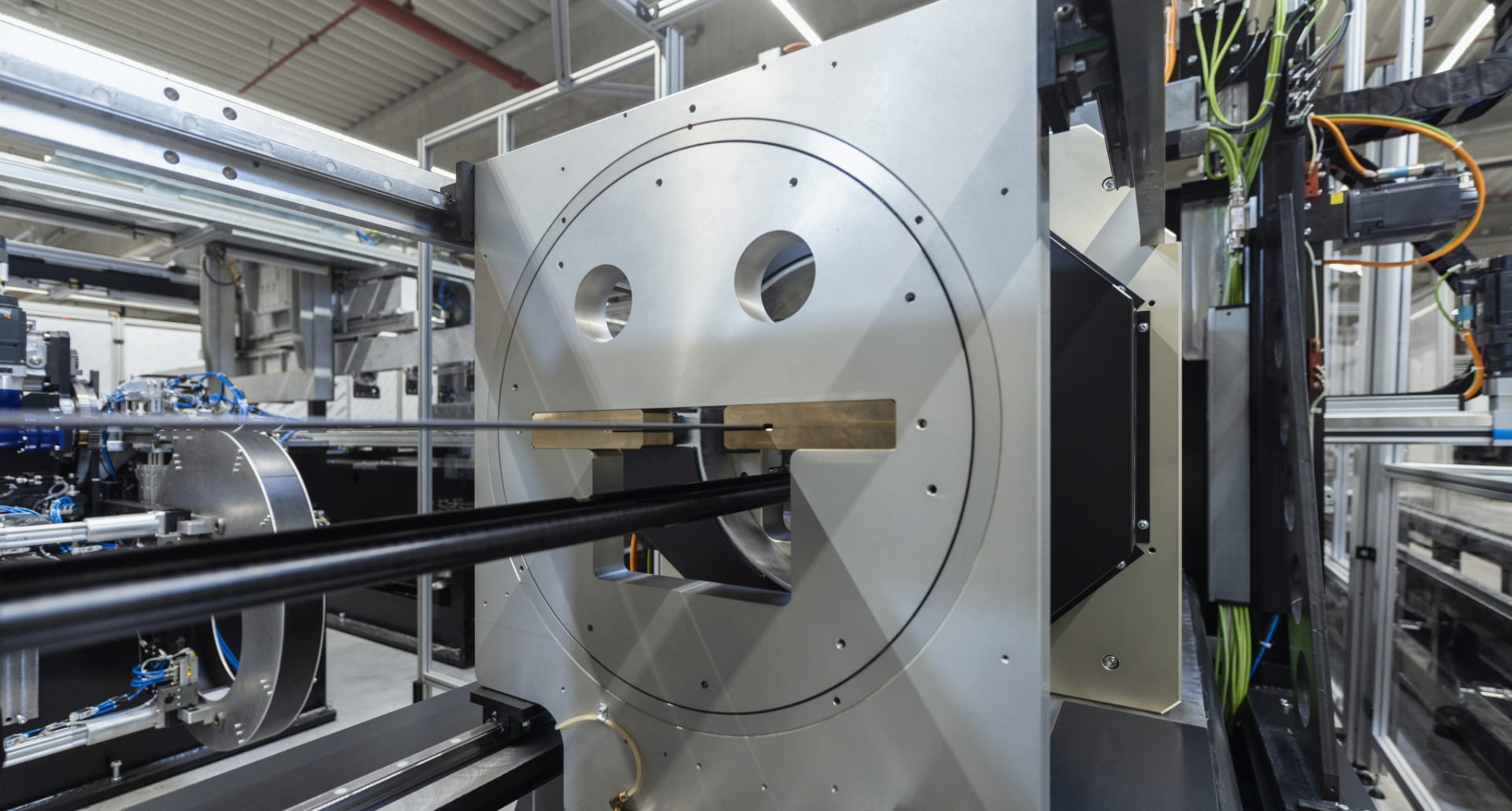
This gave us designers a great deal of leeway to design the system exactly according to our development goals.Kai-Uwe Pahl, Design Engineer at Schaeffler ELMOTEC STATOMAT
Individual bearing assemblies with wire race bearings
In order to successfully wind these stators, the flat copper wires must be laid simultaneously with one another from several directions at the same time and without causing damage to the wires. Schaeffler ELMOTEC STATOMAT achieves this by utilizing twelve Franke bearing assemblies per winding machine. The bearing assemblies are aligned and move linearly to one other. "Because we receive the bearing assemblies as complete components from Franke, we avoid sum errors in the tolerances," explains Dominik Knopp, project manager at Schaeffler ELMOTEC STATOMAT. The precision in the Franke bearing assemblies makes it possible for these machines to hold the tight tolerances required.
Franke's wire race element technology allows for custom designed assemblies – materials, dimensional flexibility, and load capacity can be individually selected for optimization. "This gave us designers a great deal of leeway to design the system exactly according to our development goals," praises designer Kai-Uwe Pahl. Another advantage of Franke wire race bearings is their compactness and high center clearance. "With the Franke bearing assemblies, it was possible to ensure sufficient space for winding without going beyond the dimensions of the entire machine. The weight aspect is also important here: Thanks to the material aluminum in the bearing housings, we reduce the moving mass, which in turn benefits precision," explains Kai-Uwe Pahl.
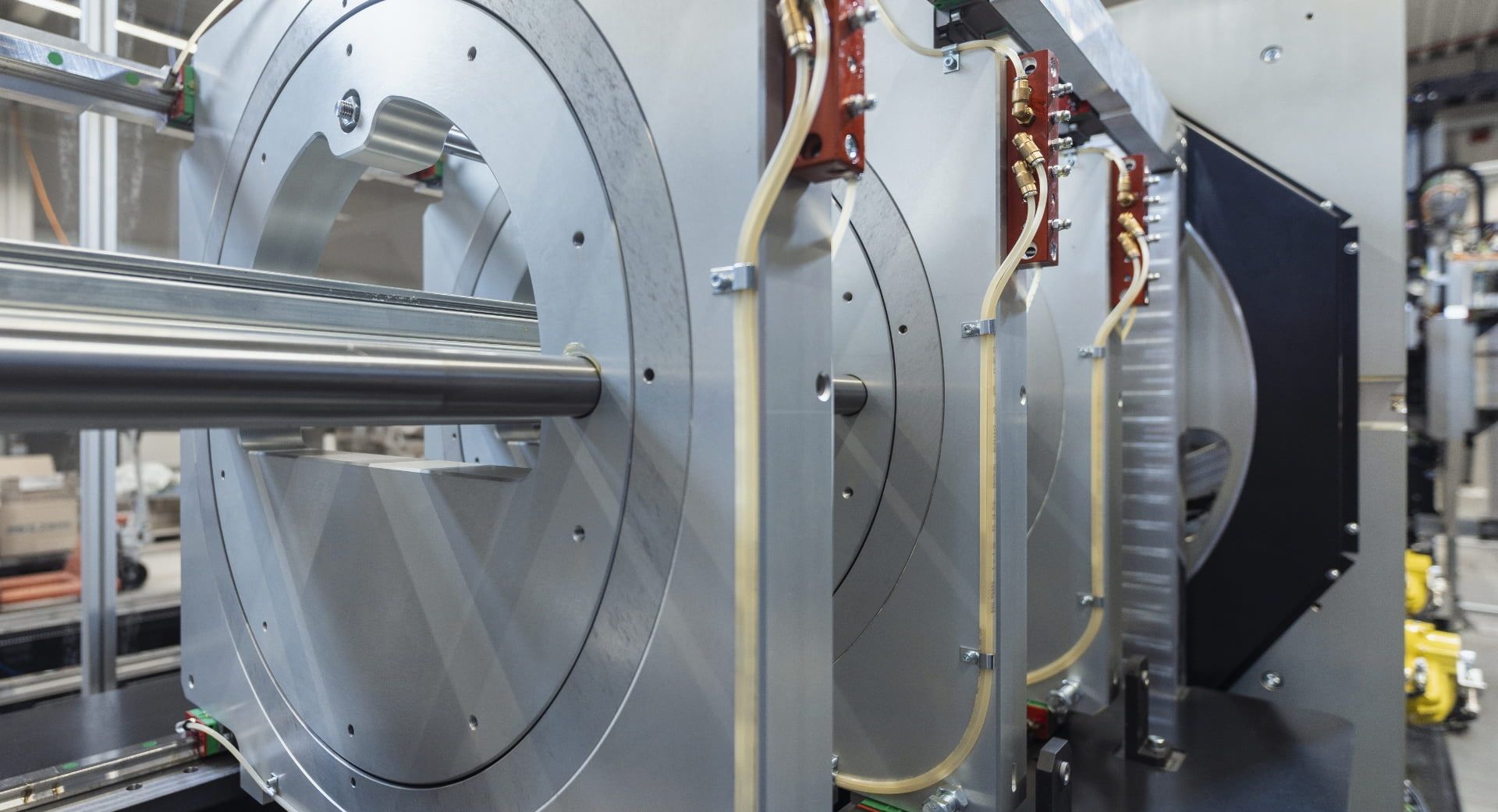
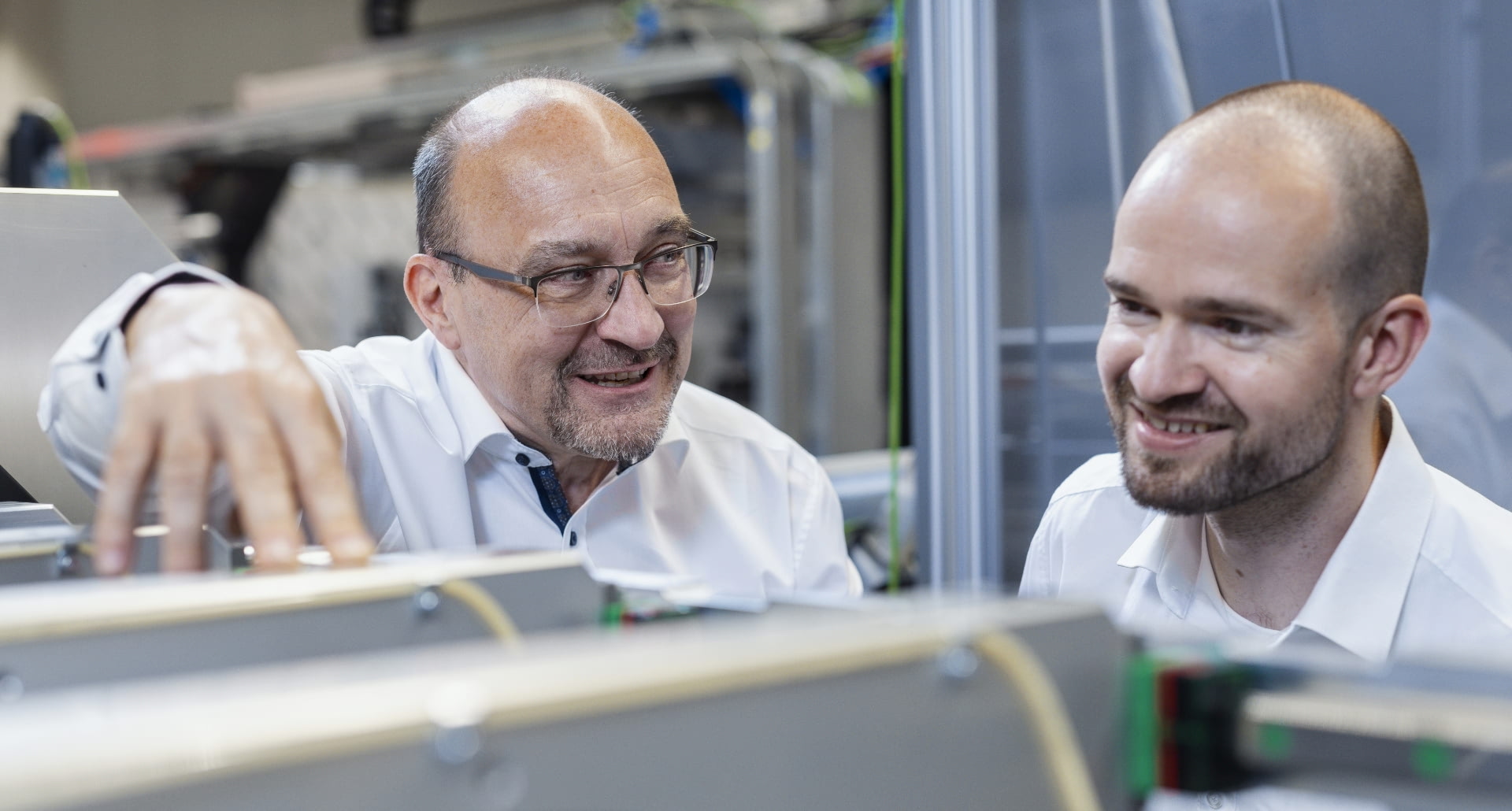
We have direct contacts at Franke for all topics. We have always received well-founded answers to our wishes and questions quickly. Franke was also an understanding partner for short-term changes in the course of the project and reacted quickly and flexibly.Dominik Knopp, Project Manager at Schaeffler ELMOTEC STATOMAT
Successful Collaboration
In order to optimize the bearing assembly designs throughout the developmental process, close collaboration between Schaeffler ELMOTEC STATOMAT and Franke was necessary. "We regularly discussed the state of affairs and all relevant stakeholders were present," says Franke commercial consultant Heike Faustmann. The two teams were very open and transparently as they handled tasks and challenges. Their open communication helped to build mutual trust and understanding.
Fast and flexible responses
Franke account manager, Michael Bärstecher, points out that Franke's skill and experience rose to meet the requirements of this demanding project. The employees involved in the project were satisfied to have successfully met the challenges and satisfied the customer’s requirements. Dominik Knopp from Schaeffler ELMOTEC STATOMAT stated: "We have direct contacts at Franke for all topics. We have always received well-founded answers to our wishes and questions quickly. Even with short-term changes in the course of the project, Franke was an understanding partner and reacted quickly and flexibly."
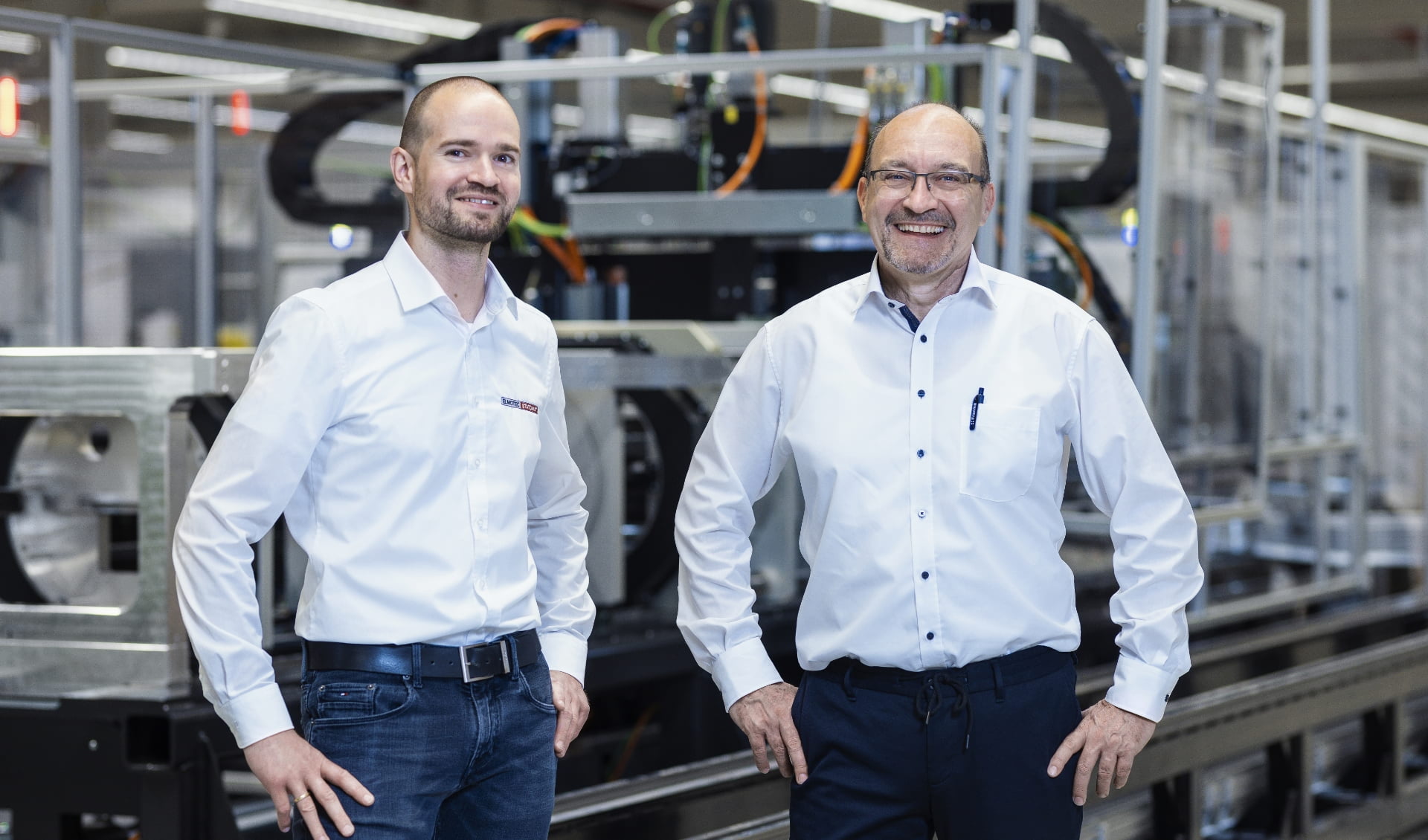
About Schaeffler ELMOTEC STATOMAT
Schaeffler ELMOTEC STATOMAT is a pioneer in coil winding technology and a leading manufacturer of special machines and precision tools for stator production. With more than 70 years of experience and more than 50 patents worldwide in stator production, Schaeffler ELMOTEC STATOMAT offers innovative and customized manufacturing solutions. A team of 160 employees at the Karben site near Frankfurt am Main is working on the realization of individual and scalable winding systems for electric motors with high copper fill factors and maximum efficiency. As part of the globally positioned Schaeffler Group and in conjunction with a strong partner network, Schaeffler ELMOTEC STATOMAT also offers comprehensive industrialization and automation expertise.
Profile about Schaeffler ELMOTEC STATOMAT
Location: Karben near Frankfurt am Main
Established: 1949
Expertise: Individual winding systems for compact electric motors with maximum efficiency
Website: www.elmotec-statomat.eu