Customer Stories
Precise cutting on a grand scale
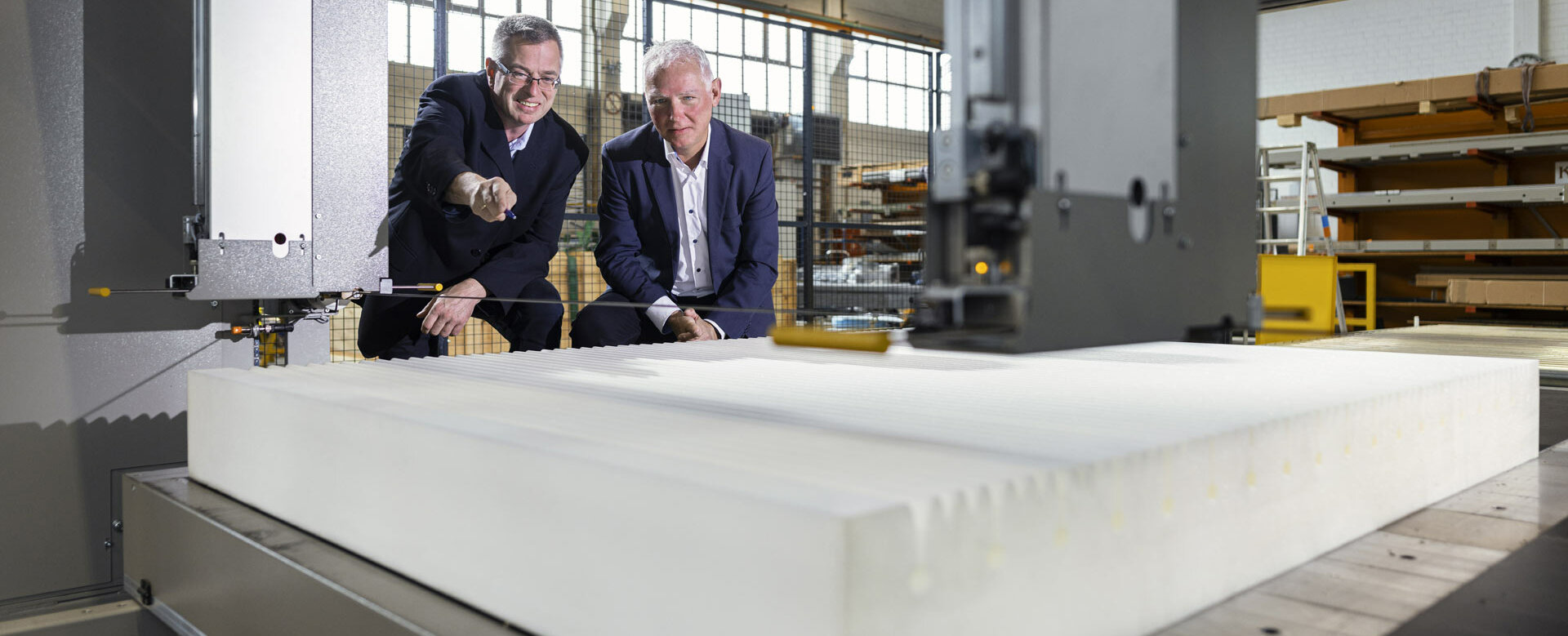
The Aachen-based family business Fecken-Kirfel has been in existence for over 150 years. And for over 100 years it has been perfecting solutions for efficient cutting on an industrial scale. Fecken-Kirfel is a world leader with its cutting machines. Lightweight Franke linear guides guide the bandknifes evenly and precisely through the material.
In 1870, Johann Fecken founded the Fecken-Kirfel company with the financial support of his father-in-law, Mr Kirfel. At the beginning, he produced machines for the cloth and wool manufacturers based in the Aachen area. Fecken-Kirfel even produced steam engines. Their power was transmitted to various production machines by means of leather belts. In order to cut the required belts efficiently, the engineers at Fecken-Kirfel developed their own mechanical solutions. Subsequently, they also designed cutting machines for rubber and cork. In the 1950s, foams, which were hardly known at the time, were rapidly spreading all over the world. Fecken-Kirfel had the know-how and supplied the machines to efficiently shape the new material. Today, foams for mattresses or upholstered furniture are the most frequently cut material with Fecken-Kirfel machines. In addition, the company also offers solutions for harder materials such as rubber, cork or technical plastics.
The bandknife principle
Almost all cutting machines from Fecken-Kirfel are based on the same principle: A continuously rotating bandknife is guided through the material to be cut and is usually also continuously ground. The company has further differentiated this principle in various machine types and brought it to perfection. Almost 50 machine types can be found on the company website under "Products". If required, the development engineers at Fecken-Kirfel can adapt them individually to the customer's task or develop new machine shapes.
Profile Franke Solutions
Franke linear guides type FDA 25
Used advantages: low weight, high dynamics, precision, long service life, freedom of maintenance
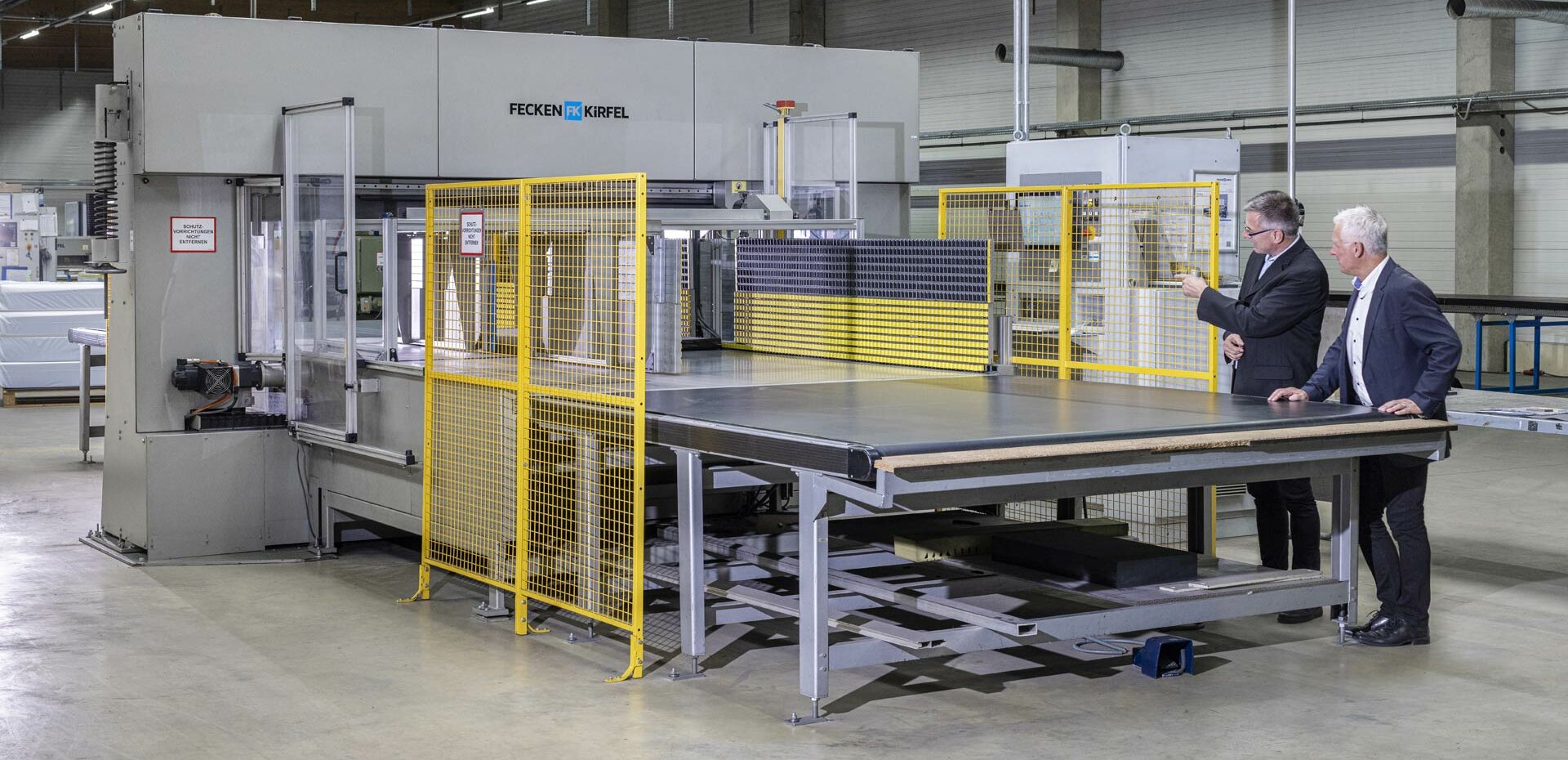
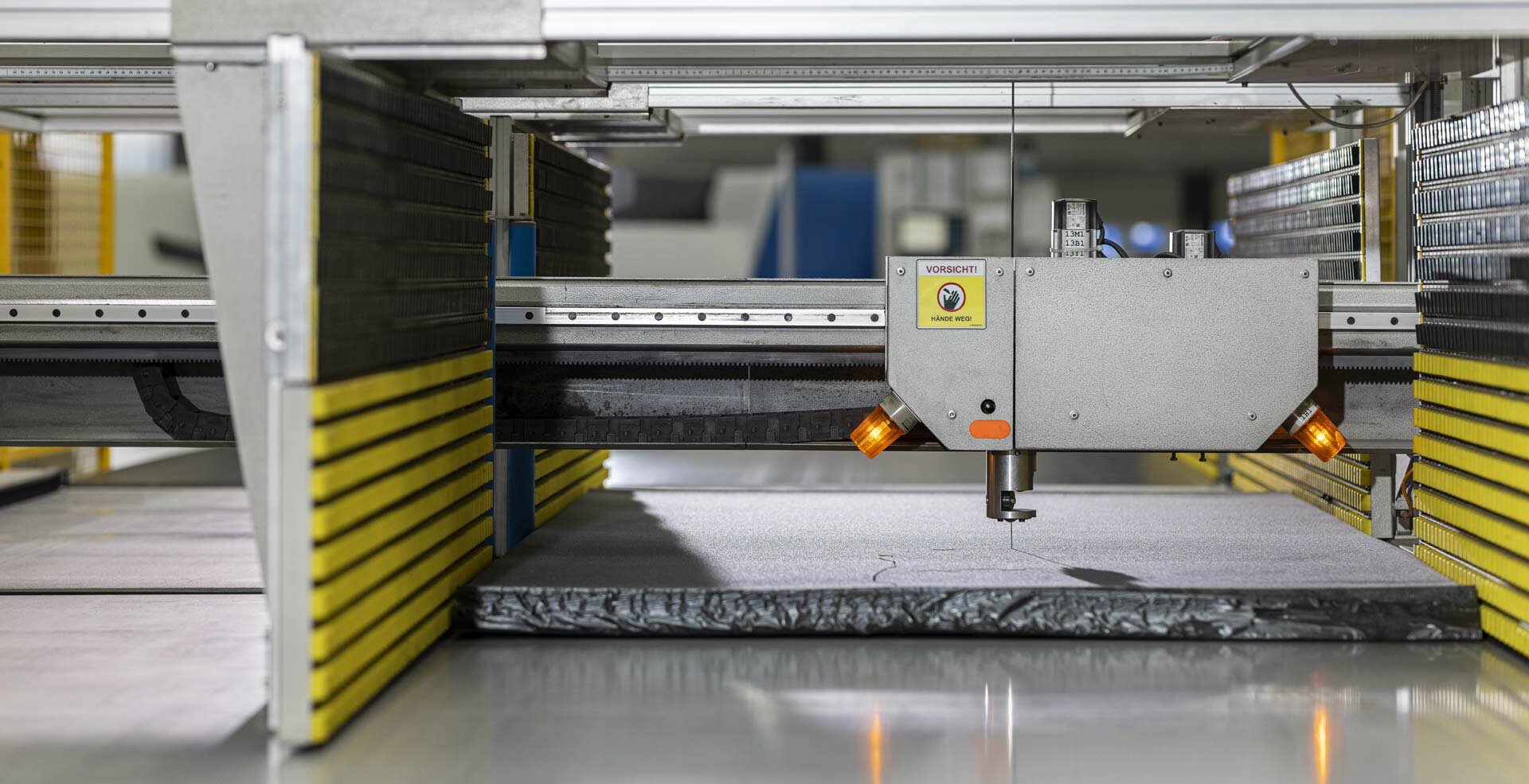
Before customers buy a machine from Fecken-Kirfel, they often want the cutting process to be tested with their material. "Test cuts are part of our daily tasks," says Michael Tillmann, technical manager and authorised signatory at Fecken-Kirfel. A cutting machine or cutting system from Fecken-Kirfel is individually designed for the respective task. For everything that can be cut by machine with a bandknife, Fecken-Kirfel offers a suitably and, if required, also an individually adapted solution.
Knowledge is the basis of success
Michael Tillmann has been with the company for 24 years. "It is part of our philosophy that managers come from our own ranks," he explains. Fecken-Kirfel attaches great importance to retaining and constantly expanding the valuable knowledge of its approximately 200 employees. With this know-how in the background, the traditional company meets the diverse tasks of its customers and new trends on the international markets every day.
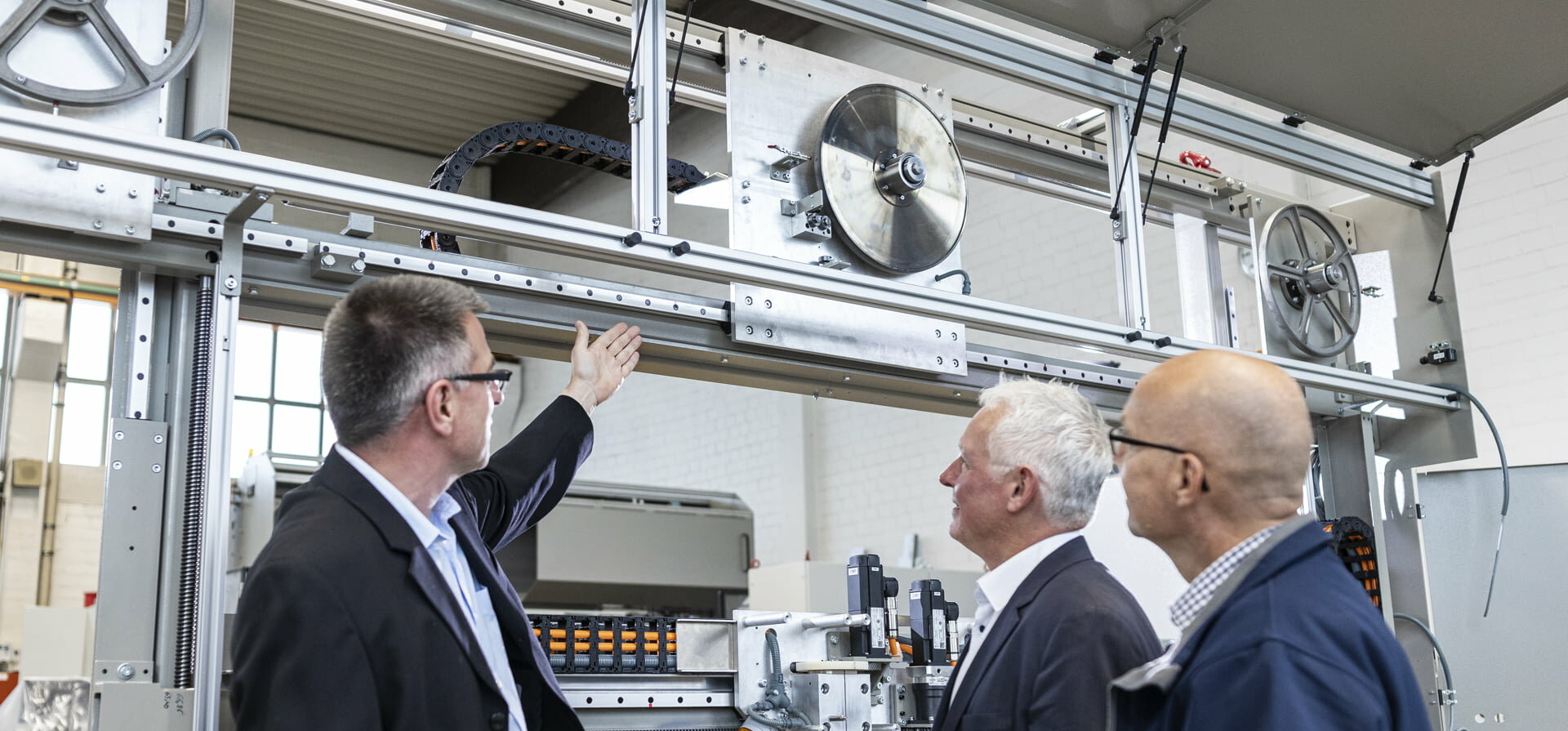
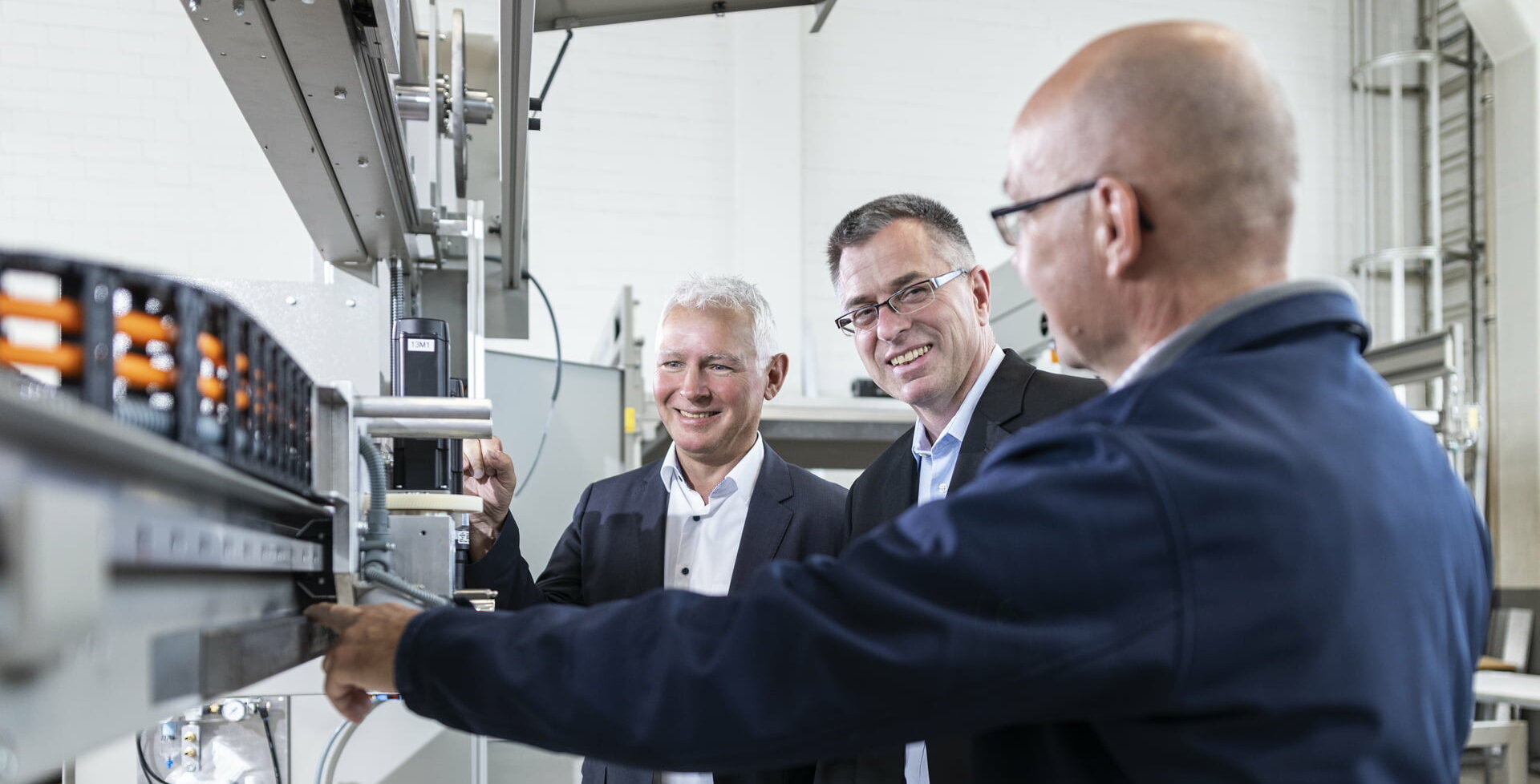
Cutting this material is not easy.Michael Tillmann, Technical Manager of Fecken-Kirfel
The challenge of memory foam
Fecken-Kirfel is proof of the thesis that consistent success is only possible through constant change. When new materials are developed, Fecken-Kirfel looks at how they could be optimally cut. As an example, Michael Tillmann mentions viscoelastic foam, also called memory foam. Originally developed as a seating material for the aerospace industry, it is now also used in earthly mattresses and upholstery. Under the influence of heat, the material adapts to the shape of the body. "Cutting this material is not easy," says Michael Tillmann. In order to achieve the best possible cutting result, he says, you have to get to grips with the specific properties of the material beforehand. After all, apart from the cut, the material should not be deformed or affected before it is used. The large volume of the material blocks to be cut often poses another challenge. The bandknife must be guided around the entire block when cutting. The larger the volume, the higher the demands on the design.
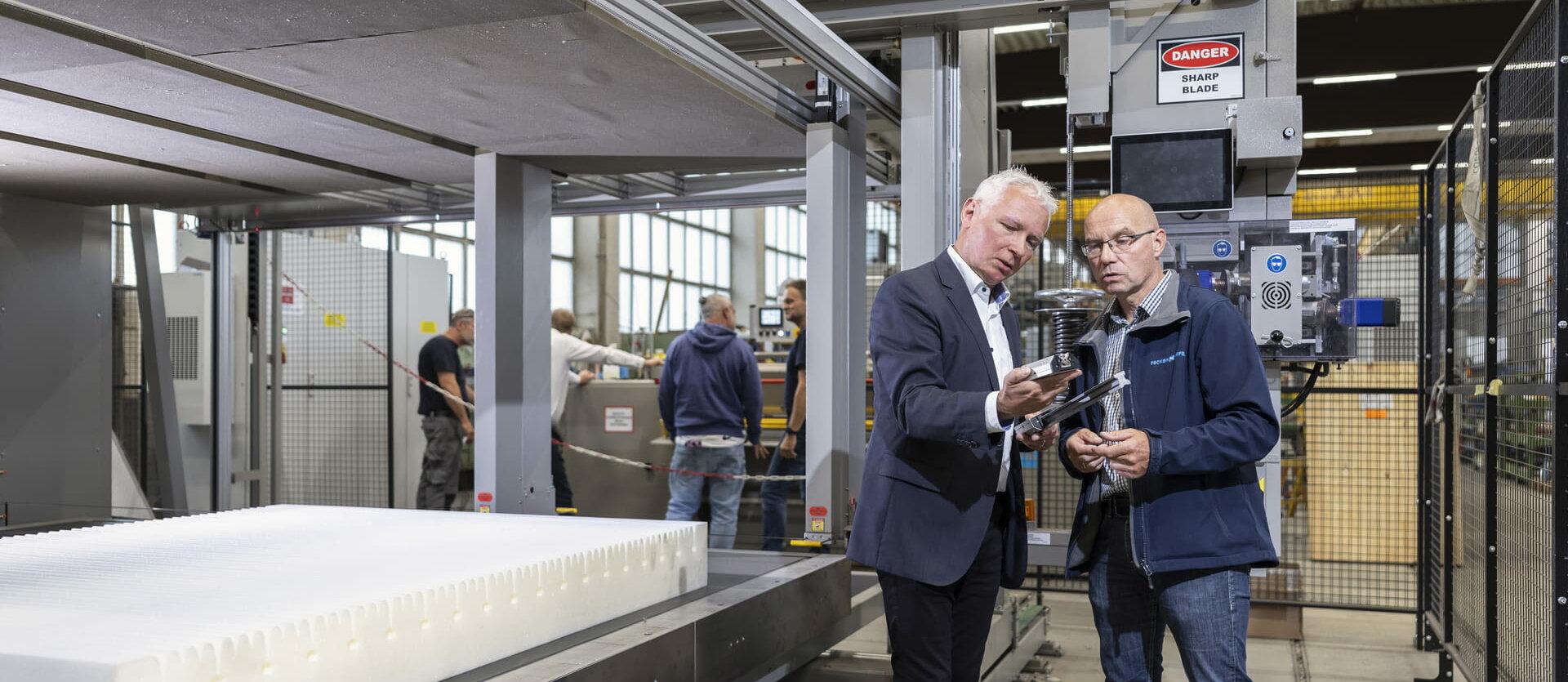
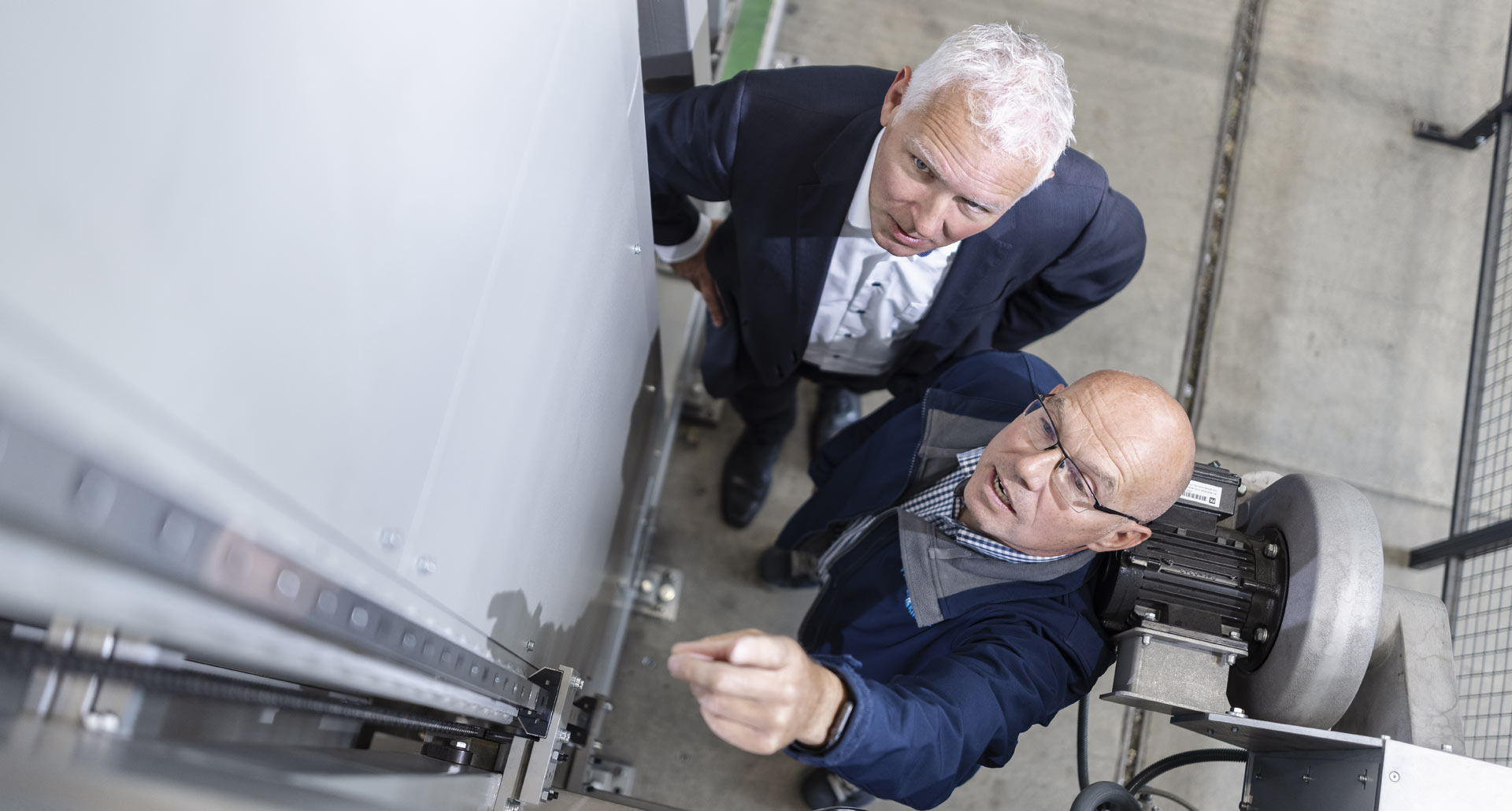
Franke linear guides for precise contours
Linear guides from Franke are installed in many cutting machines from Fecken-Kirfel. They are mainly used when not only straight edges but also precise contours have to be cut into the material. For this purpose, the bandknife must be moved in two axes and also rotated in itself. Franke linear guides are used for linear travel. "In this context, we appreciate Franke's lightweight aluminium construction," says Stefan Lennartz, head of mechanical construction at Fecken-Kirfel. Thanks to lower moving masses, greater dynamics are possible with the Franke aluminium guides.
We use the Franke guides very frequentlyStefan Lennartz, Head of the Mechanical Construction at Fecken-Kirfel
Rollers instead of balls
Instead of rotating balls, which are common in most linear guides, Franke uses rollers with bearings as rolling elements, which run on the typical Franke wire tracks. The advantages of this design for Fecken-Kirfel are high dynamics, high precision and low weight. The sliding resistance is adjustable on Franke linear guides. "We use the adjustability to adapt the guides to the application," says Stefan Lennartz. Since the roller bearings are lubricated for life, Franke linear guides are maintenance-free. "That is one point that brought us to Franke at the time," remarks Michael Tillmann. Fecken-Kirfel has been using Franke linear systems for over 30 years. "We use the Franke guideways very frequently," says Stefan Lennartz. In addition to the linear axes of the bandknifes, the device for loosening and tensioning the bandknife when changing the knife is another application.
I can't remember a time when a Franke guide had to be replaced because of a problem.Stefan Lennartz, Head of the Mechanical Construction at Fecken-Kirfel
The quality must be right
The vertical range of manufacture at Fecken-Kirfel is very high. It is part of the company's philosophy to have complete control over product quality. Of course, the same high quality standards apply to the few supplied components that Fecken-Kirfel installs. The company is very satisfied with Franke's products in terms of quality and durability, says chief designer Stefan Lennartz: "I can't remember a time when a Franke guide had to be replaced because of a problem." That is saying something, after all, he has been working at Fecken-Kirfel for 35 years.
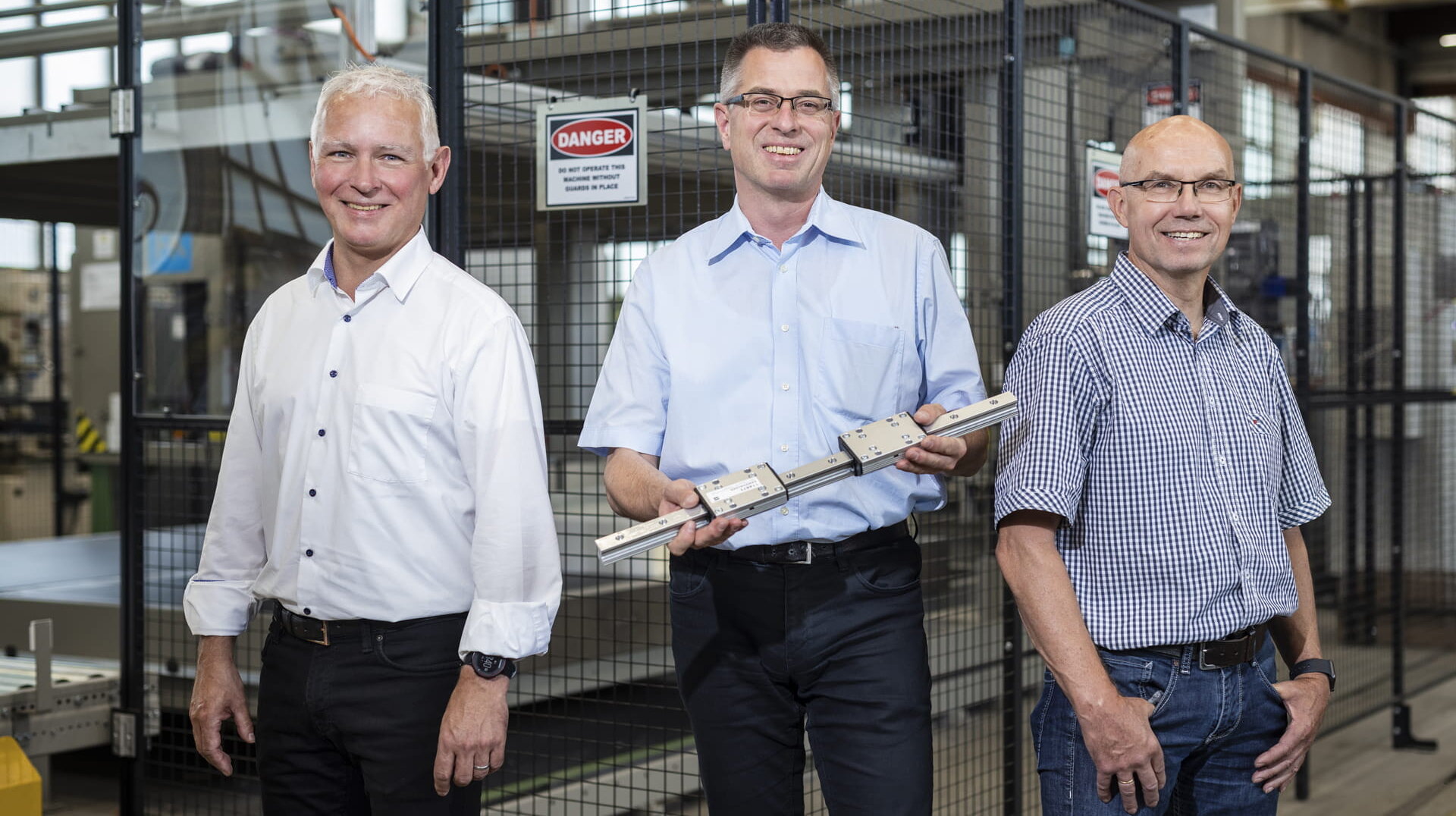
About Fecken-Kirfel
The family-owned company Fecken-Kirfel was founded in 1870 and produces precise and efficient cutting machines for processing flexible foam, compact plastics such as rubber, caoutchouc and neoprene, as well as rigid foam and cork. Fecken-Kirfel is the global technology and quality leader in cutting machines and cutting systems. All cutting machines are manufactured with a very high vertical range of manufacture at the headquarters in Aachen, Germany. Approximately 200 people are employed there.